Cuatro factores clave: Explicación de los orígenes y el desarrollo de las marcas de quemaduras en productos moldeados por inyección
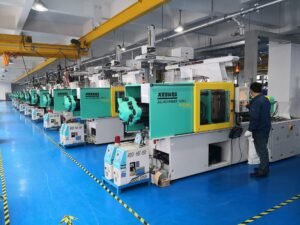
Los cuatro factores principales de las marcas de quemaduras en el moldeo por inyección
1. Factor uno: fractura por fusión
Cuando el material fundido se inyecta en una cavidad de molde relativamente grande en condiciones de alta velocidad y alta presión, es muy propenso a un fenómeno conocido como "fractura de la masa fundida". Durante este proceso, la superficie del material fundido presenta fracturas transversales, y la zona fracturada, que es rugosa, se mezcla con la capa superficial de la pieza plástica, formando lo que se conoce como "marcas de fusión". Este problema es particularmente grave cuando se inyecta directamente una pequeña cantidad de material fundido en una cavidad de molde excesivamente grande, lo que da como resultado fracturas de fusión más significativas y, en consecuencia, marcas de fusión más grandes en el producto terminado.
La esencia de la fractura por fusión se debe al comportamiento elástico de los polímeros fundidos. Cuando la masa fundida fluye dentro del barril, la masa fundida cerca de la pared del barril está sujeta a fricción, lo que resulta en una mayor tensión y una velocidad de flujo más lenta. Una vez que se inyecta la masa fundida desde la boquilla, la tensión ejercida por la pared del cilindro desaparece y la masa fundida en el centro del cilindro fluye a una velocidad extremadamente alta. La masa fundida cerca de la pared del barril es transportada y acelerada por la masa fundida central. Dado que el flujo de la masa fundida es relativamente continuo, las velocidades de flujo de las masas fundidas interna y externa se reorganizarán y tenderán hacia una velocidad promedio.
Durante este proceso, la masa fundida sufrirá un cambio brusco de tensión, lo que provocará una tensión. Debido a la velocidad de inyección extremadamente rápida, la tensión ejercida es particularmente grande, superando con creces la capacidad de deformación de la masa fundida, lo que lleva a la ruptura de la masa fundida.
Si la masa fundida encuentra cambios repentinos de forma en el canal, como constricción del diámetro, expansión o presencia de puntos muertos, la masa fundida permanece y circula en estos puntos muertos. Sus condiciones de tensión difieren de las de la masa fundida normal, con mayor deformación por corte. Cuando se vuelve a mezclar con el flujo normal y se inyecta, la recuperación de deformación inconsistente entre los dos no puede conciliarse. Si la discrepancia es significativa, se produce fractura y ruptura. Este fenómeno también se manifiesta como fractura por fusión.
De lo anterior, queda claro que para superar la fractura por fusión y evitar la aparición de motas :
En primer lugar, es importante eliminar los ángulos muertos en el sistema de canales para que los canales de flujo sean lo más racionalizados posible.
En segundo lugar, aumentar adecuadamente la temperatura del material para reducir el tiempo de relajación del material fundido, facilitando la recuperación y curación de su deformación.
El tercer enfoque consiste en añadir sustancias de bajo peso molecular a las materias primas, porque cuanto menor es el peso molecular de la masa fundida y más amplia es su distribución, más ayuda a mitigar los efectos elásticos.
El cuarto es controlar adecuadamente la velocidad de inyección y la velocidad de rotación del tornillo.
Quinto, es crucial establecer razonablemente la ubicación de la puerta y elegir la forma correcta de la misma. La práctica ha demostrado que lo ideal es utilizar una puerta puntual ampliada o una puerta submarina (puerta de túnel). La mejor ubicación para la compuerta es donde el material fundido ingresa primero a una cámara de transición antes de fluir hacia la cavidad más grande, en lugar de permitir que el material fluya directamente hacia la cavidad más grande.
2. Factor dos: control inadecuado de las condiciones de moldeo
Esta también es una causa importante de quemaduras y quemaduras en la superficie de las piezas de plástico, especialmente la magnitud de la velocidad de inyección tiene un impacto considerable. Cuando el material fundido se inyecta en la cavidad del molde a un ritmo lento, el estado de flujo de la masa fundida es laminar; A medida que la velocidad de inyección aumenta hasta cierto nivel, el estado de flujo pasa gradualmente a flujo turbulento.
En circunstancias normales, la superficie de las piezas de plástico formadas en condiciones de flujo laminar tiende a ser brillante y suave, mientras que las formadas en condiciones turbulentas no sólo son propensas a tener imperfecciones en la superficie sino que también es probable que tengan bolsas de aire dentro de las piezas. Por tanto, la velocidad de inyección no debe ser demasiado alta; es aconsejable controlar el flujo del material para llenar el molde en estado laminar.
Si la temperatura de la masa fundida es demasiado alta, puede provocar fácilmente su descomposición y carbonización, lo que provocará manchas quemadas en la superficie de las piezas de plástico. Generalmente, la velocidad del tornillo de una máquina de moldeo por inyección debe ser inferior a 90 rpm y la contrapresión debe ser inferior a 2 MPa, para evitar un calor excesivo por fricción en el cilindro.
Si se genera calor por fricción excesivo durante el proceso de moldeo debido a que el tiempo de rotación del tornillo es demasiado largo mientras se retrae, se puede superar aumentando adecuadamente la velocidad del tornillo, extendiendo el ciclo de moldeo, reduciendo la contrapresión del tornillo, elevando la temperatura de alimentación. sección del cañón y utilizando materiales con poca lubricidad.
Durante el proceso de inyección, el reflujo excesivo de la masa fundida a lo largo de las ranuras del tornillo y la retención de resina en la válvula de retención pueden provocar la degradación y descomposición de la masa fundida. Para solucionar este problema, es aconsejable utilizar resinas con mayor viscosidad, reducir adecuadamente la presión de inyección y cambiar a máquinas de moldeo por inyección con una mayor relación longitud-diámetro. Las válvulas antirretorno utilizadas habitualmente en las máquinas de moldeo por inyección son bastante propensas a provocar retención, lo que provoca descomposición y decoloración. Cuando la masa fundida descompuesta y descolorida se inyecta en la cavidad del molde, puede formar marcas de quemaduras negras o del color del té. Para evitarlo, se debe limpiar periódicamente el sistema de tornillos centrado alrededor de la boquilla.
3. Factor tres: mal funcionamiento del molde
Si los orificios de ventilación del molde están bloqueados por agentes desmoldantes o depósitos solidificados de las materias primas, si la configuración de ventilación es insuficiente o está mal colocada, o si la velocidad de llenado del molde es demasiado rápida, el aire atrapado dentro del molde puede sufrir una compresión adiabática, generando Gases de alta temperatura que pueden provocar la descomposición y carbonización de la resina. Para solucionar esto, se deben eliminar las obstrucciones, se debe reducir la fuerza de sujeción y se debe mejorar la mala ventilación del molde.
La determinación de la forma y posición de la puerta del molde también es muy importante. Durante el proceso de diseño, es necesario considerar completamente el estado de flujo del material fundido y el rendimiento de escape del molde.
Además, la cantidad de agente desmoldante utilizado no debe ser excesiva y la superficie de la cavidad del molde debe mantenerse con un alto grado de suavidad.
4. Factor cuatro: las materias primas no cumplen los requisitos
Si las materias primas contienen un nivel demasiado alto de humedad y sustancias volátiles, o si el índice de flujo de fusión es demasiado alto, o si se utiliza una cantidad excesiva de lubricante, esto puede provocar defectos por quemaduras y marcas de quemaduras.
Para ello, las materias primas deben tratarse con un secador de tolva u otros métodos de presecado, cambiar a resinas con un índice de fusión más bajo y reducir la cantidad de lubricante utilizado.