PRODUCTS
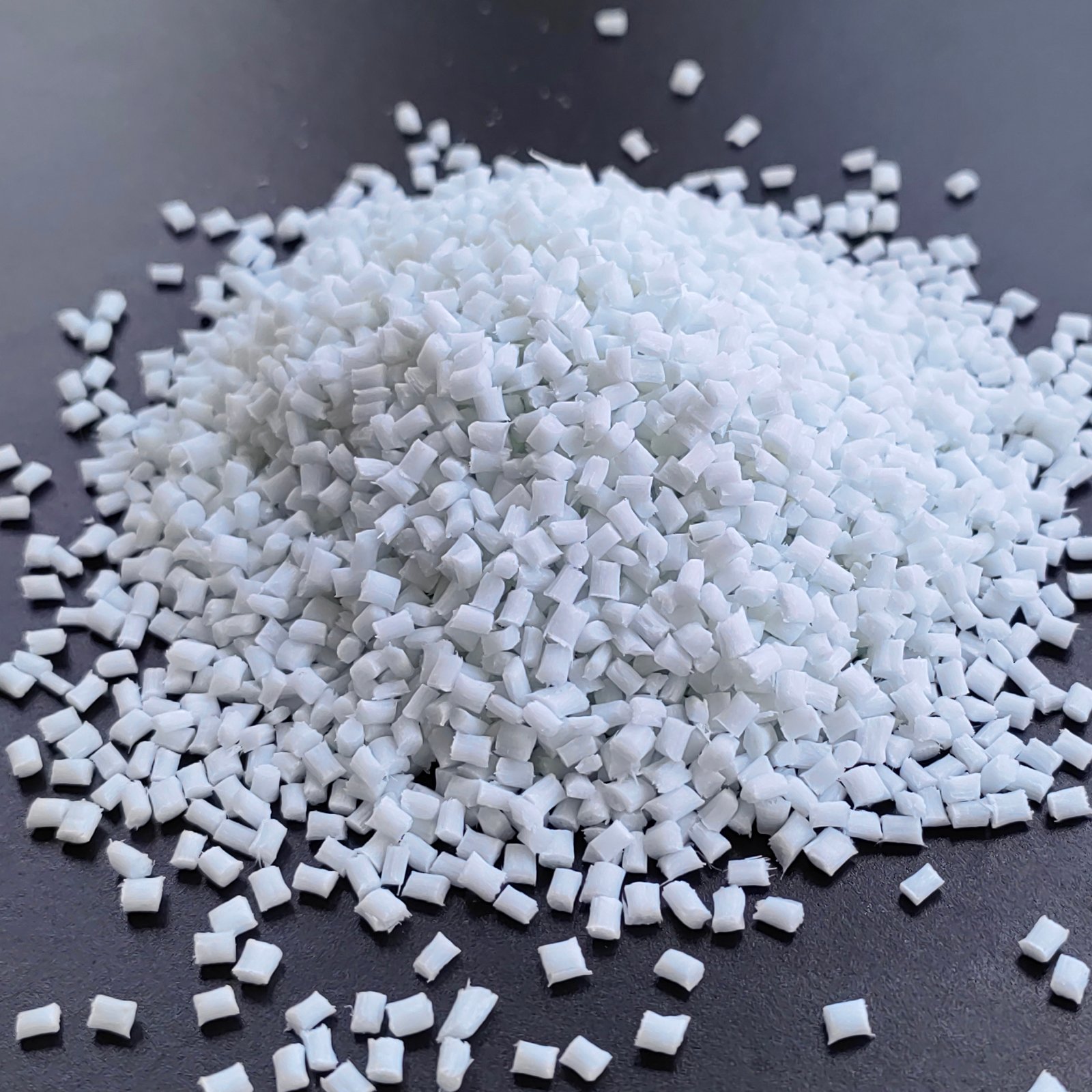
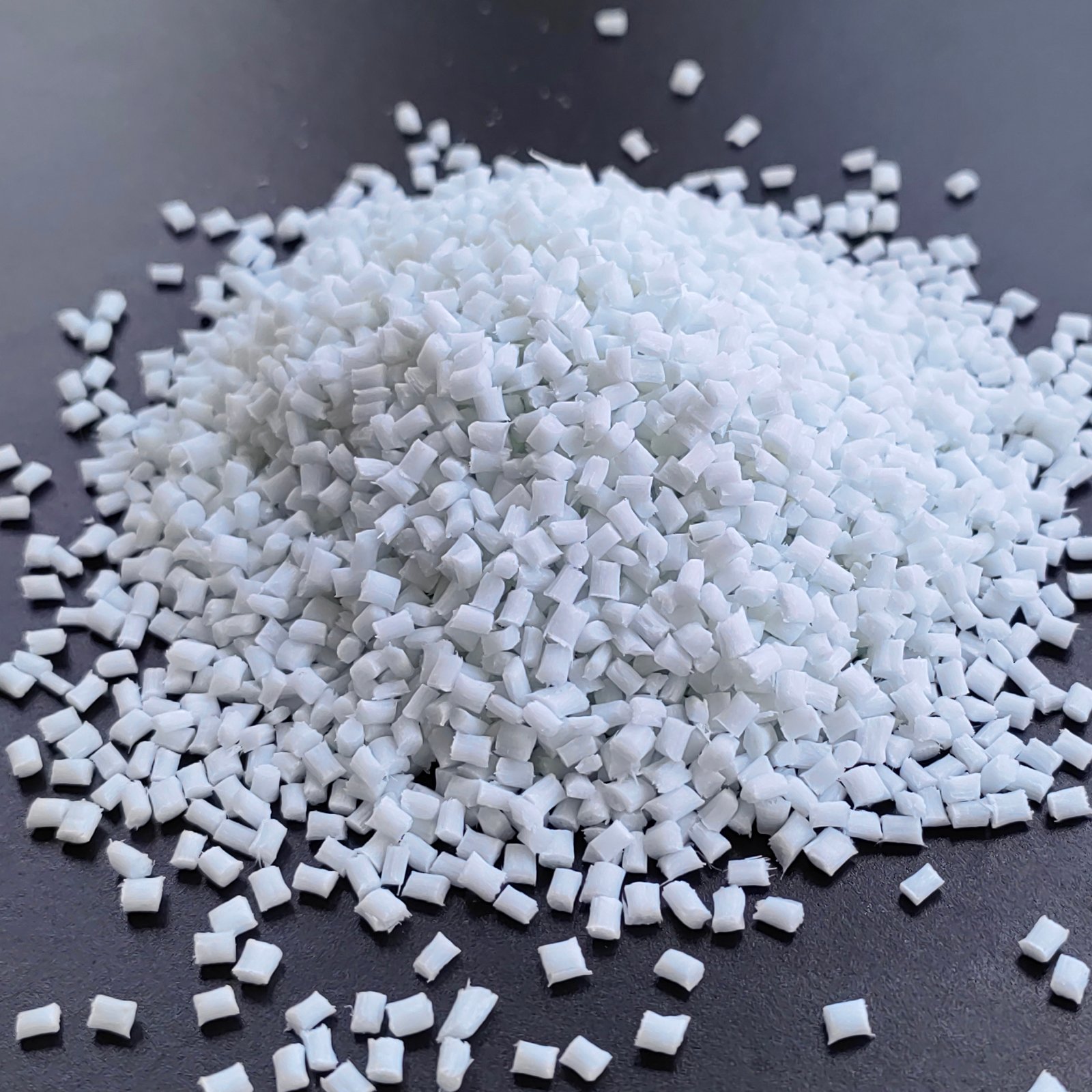
BASF Polyoxymethylene Plastic H4320 AT Detailed Introduction
Product Struction
What is Polyoxymethylene Plastic H4320 AT?
Polyformaldehyde plastic have attracted extensive attention in the field of materials science for their unique properties. POM H4320 AT has significant advantages as a semi-finished high molecular weight extruded plastic particles. Its ability to extrude thick-walled products at high yields makes it excellent in the manufacture of thick-walled components, meeting the needs of relevant industrial sectors for efficient production and specific structures.
From the point of view of material properties, POM H4320 AT is extrusion grade and heat stable, the additive contains release agents, and the processing method includes injection molding and extrusion molding, which provides flexibility for its application in different production processes. As a copolymer, POM H4320 AT also has the characteristics of color stability, high thermal stability, fade resistance, etc., to ensure the long-term performance of the product in complex environments.
Polyformaldehyde plastic POM H4320 AT is a highly crystalline polymer with excellent mechanical properties, its hardness, strength and stiffness are similar to metal, and it is one of the materials whose mechanical properties are closest to metal in engineering plastics. High bonding energy and high cohesion energy make it have good wear resistance, the uncrystallized part gathers on the spherulite surface, plays a lubricating role, effectively reduces friction and wear, and further expands its application scenario. Whether in machinery manufacturing or daily product production, polyformaldehyde plastic provide a strong support for industrial development with their unique properties.
Polyoxymethylene Plastic H4320 AT Datasheet
Mechanical behavior | Condition | Standard | Value | Unit | |||
Elongation | Yield | ISO 527 | 11 | % | |||
Elongation | Break | ISO 527 | 31 | % | |||
Tensile Strength | Yield | ISO 527 | 60 | MPa | |||
Tensile Modulus | ISO 527 | 2400 | MPa | ||||
Tensile Creep Modulus | 1hr | ISO 899 | 1800 | MPa | |||
Tensile Creep Modulus | 1000hr | ISO 899 | 1300 | MPa | |||
Charpy Un-notch Impact | -30°C | ISO 179 | 250 | kJ/m² | |||
Charpy Notch Impact | 23°C | ISO 179 | 6.5 | kJ/m² | |||
Charpy Notch Impact | -30°C | ISO 179 | 5.5 | kJ/m² | |||
Thermal | Condition | Standard | Value | Unit | |||
HDT | 1.8MPa | ISO 75 | 90 | °C | |||
HDT | 0.45MPa | ISO 75 | 155 | °C | |||
Melting Temperature | 10°C/min | ISO 11357 | 163 | °C | |||
CLE | Flow | ISO 11359 | 1.2E-4 | cm/cm/°C | |||
Vicat Softening Temperature | 50°C/hr 50N | ISO 306 | 150 | °C | |||
Physical property | Condition | Standard | Value | Unit | |||
Water Absorption | ISO 62 | 1 | % | ||||
Humidity Absorption | ISO 62 | 0.25 | % | ||||
Shrinkage | Flow | ISO 294 | 2.2 | % | |||
Shrinkage | xFlow | ISO 294 | 2.1 | % | |||
Density | ISO 1183 | 1400 | kg/m³ | ||||
Melt Index | 190°C 2.16kg | ISO 1133 | 2.2 | cm³/10min | |||
Electrical properties | Condition | Standard | Value | Unit | |||
CTI | IEC 60112 | 600 | V | ||||
Dielectric Constant | 100Hz | IEC 62631-2-1 | 3.8 | ||||
Dielectric Constant | 1MHz | IEC 62631-2-1 | 3.8 | ||||
Volume Resistivity | IEC 62631 | 1E11 | Ω.m | ||||
Dielectric Strength | IEC 60243 | 40 | KV/mm | ||||
Dissipation Factor | 100Hz | IEC 62631-2-1 | 0.001 | ||||
Dissipation Factor | 1MHz | IEC 62631-2-1 | 0.005 | ||||
Surface Resistivity | IEC 62631-3-2 | 1E13 | Ω | ||||
Flammability | Condition | Standard | Value | Unit | |||
Limiting oxygen index | ISO 4589 | 15 | % | ||||
Flame Rating | 1.6mm | UL94 | HB | ||||
Flame Rating | 0.8mm | UL94 | HB |
Click here to download TDS for POM H4320 AT
Polyoxymethylene Plastic H4320 AT Appearance
Want to learn more? Get the TDS and request a free sample—contact us today!
【Related Recommendations】
POM W2320 0035: Low-VOC Acetal Copolymer for Complex Injection Molding Learn more>
POM FM025E: High-Viscosity Acetal for Durable Precision Components Learn more>
POM FM270: High-Flow Acetal Copolymer for Automotive & Electronics Learn more>