Four Key Factors: Explaining the Origins and Development of Burn Marks on Injection Molded Products
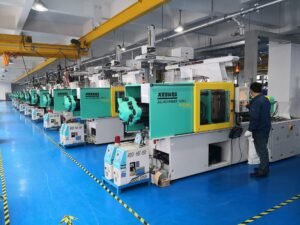
The Four Major Factors of Injection Molding Burn Marks
1. Factor One: Melt Fracture
When the molten material is injected into a relatively large mold cavity under high-speed and high-pressure conditions, it is highly prone to a phenomenon known as "melt fracture." During this process, the surface of the molten material exhibits transverse fractures, and the fractured area, which is rough, gets mixed into the surface layer of the plastic part, forming what is known as "melt marks." This issue is particularly severe when a small amount of molten material is directly injected into an excessively large mold cavity, resulting in more significant melt fractures and correspondingly larger melt marks on the finished product.
The essence of melt fracture is due to the elastic behavior of polymer melts. When the melt flows inside the barrel, the melt near the barrel wall is subjected to friction, resulting in higher stress and slower flow velocity. Once the melt is injected from the nozzle, the stress exerted by the barrel wall disappears, and the melt in the center of the barrel flows at an extremely high velocity. The melt near the barrel wall is carried and accelerated by the central melt. Since the flow of the melt is relatively continuous, the flow velocities of the internal and external melts will rearrange and tend toward an average velocity.
During this process, the melt will undergo a sharp change in stress, resulting in strain. Due to the extremely fast injection speed, the stress exerted is particularly great, far exceeding the melt's capacity to strain, leading to the rupture of the melt.
If the melt encounters sudden shape changes in the runner, such as diameter constriction, expansion, or the presence of dead spots, the melt lingers and circulates in these dead spots. Its stress conditions differ from those of the normal melt, with greater shear deformation. When it mixes back into the normal flow and is injected, the inconsistent deformation recovery between the two cannot reconcile. If the discrepancy is significant, fracture and rupture occur. This phenomenon is also manifested as melt fracture.
From the above, it is clear that to overcome melt fracture and avoid the occurrence of specks :
Firstly, it is important to eliminate dead angles in the runner system to make the flow channels as streamlined as possible.
Secondly, appropriately increase the temperature of the material to reduce the relaxation time of the molten material, making it easier for its deformation to recover and heal.
The third approach is to add low molecular weight substances to the raw materials, because the lower the molecular weight of the melt, and the wider its distribution, the more it helps to mitigate the elastic effects.
The fourth is to appropriately control the injection speed and screw rotation speed.
Fifth, it is crucial to reasonably set the location of the gate and choose the correct form of the gate. Practice has shown that using an enlarged point gate or a submarine gate (tunnel gate) is quite ideal. The best location for the gate is where the molten material first enters a transition chamber before flowing into the larger cavity, rather than allowing the material to flow directly into the larger cavity.
2. Factor Two: Improper Control of Molding Conditions
This is also a significant cause of scorching and burn marks on the surface of plastic parts, especially the magnitude of injection speed has a considerable impact. When the molten material is injected into the mold cavity at a slow rate, the flow state of the melt is laminar; as the injection speed increases to a certain level, the flow state gradually transitions to turbulent flow.
Under normal circumstances, the surface of plastic parts formed under laminar flow conditions tends to be bright and smooth, whereas those formed under turbulent conditions not only are prone to surface blemishes but also are likely to have air pockets inside the parts. Therefore, the injection speed should not be too high; it is advisable to control the flow of the material to fill the mold in a laminar state.
If the temperature of the melt is too high, it can easily lead to decomposition and charring of the melt, resulting in burnt spots on the surface of the plastic parts. Generally, the screw speed of an injection molding machine should be less than 90 rpm, and the back pressure should be less than 2 MPa, to avoid excessive frictional heat in the barrel.
If excessive frictional heat is generated during the molding process due to the screw's rotation time being too long while retracting, it can be overcome by appropriately increasing the screw speed, extending the molding cycle, reducing the screw back pressure, raising the temperature of the feeding section of the barrel, and using materials with poor lubricity.
During the injection process, excessive backflow of the melt along the screw grooves and resin retention at the non-return valve can lead to degradation and decomposition of the melt. To address this, it is advisable to use resins with higher viscosity, appropriately reduce the injection pressure, and switch to injection molding machines with a larger length-to-diameter ratio. The non-return valves commonly used in injection molding machines are quite prone to causing retention, leading to decomposition and discoloration. When the decomposed and discolored melt is injected into the mold cavity, it may form tea-colored or black burn marks. To prevent this, the screw system centered around the nozzle should be cleaned regularly.
3. Factor Three: Mold Malfunction
If the mold vent holes are blocked by release agents or solidified deposits from the raw materials, if the venting setup is insufficient or improperly positioned, or if the mold filling speed is too fast, the trapped air within the mold can undergo adiabatic compression, generating high-temperature gases that can cause resin decomposition and charring. To address this, blockages should be cleared, clamping force should be reduced, and the mold's poor venting should be improved.
The determination of the form and position of the mold gate is also quite important. During the design process, it is necessary to fully consider the flow state of the molten material and the exhaust performance of the mold.
Additionally, the amount of release agent used should not be excessive, and the surface of the mold cavity must be maintained with a high degree of smoothness.
4. Factor Four: Raw Materials Do Not Meet Requirements
If the raw materials contain too high a level of moisture and volatile substances, or if the melt flow index is too high, or if an excessive amount of lubricant is used, this can lead to scorching and burn marks defects.
For this, raw materials should be treated with a hopper dryer or other pre-drying methods, switch to resins with a lower melt index, and reduce the amount of lubricant used.