Четыре ключевых фактора: Объяснение происхождения и развития следов ожогов на изделиях, полученных литьем под давлением.
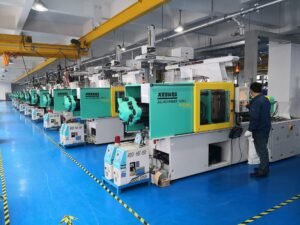
Четыре основных фактора образования следов ожогов при литье под давлением
1. Фактор первый: разрушение расплава
Когда расплавленный материал впрыскивается в относительно большую полость формы при высокой скорости и высоком давлении, он очень склонен к явлению, известному как «разрушение расплава». Во время этого процесса на поверхности расплавленного материала появляются поперечные трещины, а шероховатая область излома смешивается с поверхностным слоем пластиковой детали, образуя так называемые «следы плавления». Эта проблема становится особенно серьезной, когда небольшое количество расплавленного материала впрыскивается непосредственно в слишком большую полость формы, что приводит к более значительным трещинам расплава и, соответственно, более крупным следам расплава на готовом изделии.
Сущность разрушения расплава обусловлена упругим поведением расплавов полимеров. Когда расплав течет внутри цилиндра, расплав вблизи стенки цилиндра подвергается трению, что приводит к более высокому напряжению и снижению скорости потока. Как только расплав впрыскивается из сопла, напряжение, оказываемое стенкой цилиндра, исчезает, и расплав в центре цилиндра течет с чрезвычайно высокой скоростью. Расплав у стенки ствола переносится и ускоряется центральным расплавом. Поскольку течение расплава относительно непрерывное, скорости течения внутреннего и внешнего расплавов будут перестраиваться и стремиться к средней скорости.
В ходе этого процесса расплав претерпевает резкое изменение напряжения, приводящее к деформации. Из-за чрезвычайно высокой скорости впрыска возникающее напряжение особенно велико, намного превышая способность расплава деформироваться, что приводит к разрыву расплава.
Если расплав сталкивается с внезапными изменениями формы в желобе, например, сужением диаметра, расширением или наличием мертвых зон, расплав задерживается и циркулирует в этих мертвых зонах. Его напряженные условия отличаются от условий нормального расплава большей сдвиговой деформацией. Когда он снова смешивается с нормальным потоком и впрыскивается, непоследовательное восстановление деформации между ними не может быть согласовано. Если расхождение существенное, происходит перелом и разрыв. Это явление также проявляется в виде разрушения расплава.
Из вышеизложенного ясно, что для преодоления разрушения расплава и предотвращения появления пятен :
Во-первых, важно устранить мертвые углы в системе направляющих, чтобы сделать каналы потока максимально обтекаемыми.
Во-вторых, соответствующим образом увеличьте температуру материала, чтобы уменьшить время релаксации расплавленного материала, что облегчит восстановление и заживление его деформации.
Третий подход заключается в добавлении в сырье низкомолекулярных веществ, поскольку чем меньше молекулярная масса расплава и чем шире его распределение, тем в большей степени это способствует смягчению упругих эффектов.
Четвертый – правильно контролировать скорость впрыска и скорость вращения шнека.
В-пятых, крайне важно разумно задать расположение ворот и выбрать правильную форму ворот. Практика показала, что использование увеличенных точечных ворот или подводных ворот (туннельных ворот) вполне идеально. Лучшее место для литника - это место, где расплавленный материал сначала попадает в переходную камеру, а затем перетекает в большую полость, вместо того, чтобы позволить материалу течь непосредственно в большую полость.
2. Фактор второй: неправильный контроль условий формования.
Это также является серьезной причиной появления пригаров и следов ожогов на поверхности пластиковых деталей, особенно значительное влияние оказывает величина скорости впрыска. Когда расплавленный материал впрыскивается в полость формы с низкой скоростью, состояние течения расплава является ламинарным; по мере увеличения скорости впрыска до определенного уровня состояние течения постепенно переходит в турбулентное течение.
В нормальных условиях поверхность пластиковых деталей, сформированных в условиях ламинарного потока, имеет тенденцию быть блестящей и гладкой, тогда как детали, изготовленные в турбулентных условиях, не только склонны к появлению дефектов на поверхности, но также могут иметь воздушные карманы внутри деталей. Поэтому скорость впрыска не должна быть слишком высокой; целесообразно контролировать поток материала для заполнения формы в ламинарном состоянии.
Если температура расплава слишком высока, это легко может привести к разложению и обугливанию расплава, в результате чего на поверхности пластиковых деталей появятся подгоревшие пятна. Как правило, скорость шнека термопластавтомата должна быть менее 90 об/мин, а противодавление должно быть менее 2 МПа, чтобы избежать чрезмерного нагревания при трении в цилиндре.
Если в процессе формования образуется чрезмерное тепло трения из-за слишком длительного вращения шнека при втягивании, его можно преодолеть, соответствующим образом увеличив скорость шнека, продлив цикл формования, уменьшив противодавление шнека, повысив температуру подачи. секции ствола и использование материалов с плохой смазывающей способностью.
В процессе литья чрезмерное обратное течение расплава по винтовым канавкам и задержка смолы на обратном клапане могут привести к деградации и разложению расплава. Чтобы решить эту проблему, рекомендуется использовать смолы с более высокой вязкостью, соответствующим образом снизить давление впрыска и перейти на термопластавтоматы с большим соотношением длины к диаметру. Обратные клапаны, обычно используемые в машинах для литья под давлением, весьма склонны к задержке, что приводит к разложению и обесцвечиванию. Когда разложившийся и обесцвеченный расплав впрыскивается в полость формы, на нем могут образовываться следы чайного цвета или черные прижоги. Чтобы предотвратить это, следует регулярно чистить винтовую систему вокруг насадки.
3. Фактор третий: неисправность пресс-формы
Если вентиляционные отверстия формы заблокированы разделительным составом или затвердевшими отложениями сырья, если система вентиляции недостаточна или неправильно расположена, или если скорость заполнения формы слишком высока, захваченный воздух внутри формы может подвергаться адиабатическому сжатию, вызывая высокотемпературные газы, которые могут вызвать разложение и обугливание смолы. Чтобы решить эту проблему, следует устранить засоры, уменьшить усилие зажима и улучшить плохую вентиляцию формы.
Определение формы и положения литника формы также весьма важно. В процессе проектирования необходимо полностью учитывать текучесть расплавленного материала и характеристики выхлопа формы.
Кроме того, количество используемого разделительного состава не должно быть чрезмерным, а поверхность полости формы должна сохранять высокую степень гладкости.
4. Фактор четвертый: сырье не соответствует требованиям
Если в сырье содержится слишком высокий уровень влаги и летучих веществ, или если индекс текучести расплава слишком высок, или если используется чрезмерное количество смазки, это может привести к подгораниям и дефектам прижогов.
Для этого сырье следует обработать бункерной сушилкой или другими методами предварительной сушки, перейти на смолы с меньшим индексом плавления, уменьшить количество используемой смазки.