Vier sleutelfactoren: Uitleg over de oorsprong en ontwikkeling van brandplekken op spuitgegoten producten
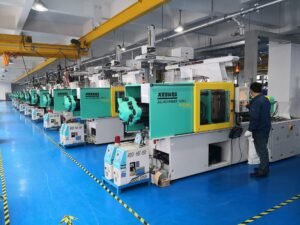
De vier belangrijkste factoren bij het spuitgieten van brandplekken
1. Factor één: smeltbreuk
Wanneer het gesmolten materiaal onder hoge snelheid en hoge druk in een relatief grote vormholte wordt geïnjecteerd, is het zeer gevoelig voor een fenomeen dat bekend staat als "smeltbreuk". Tijdens dit proces vertoont het oppervlak van het gesmolten materiaal transversale breuken, en het gebroken gebied, dat ruw is, wordt vermengd met de oppervlaktelaag van het plastic onderdeel, waardoor zogenaamde "smeltsporen" ontstaan. Dit probleem is vooral ernstig wanneer een kleine hoeveelheid gesmolten materiaal rechtstreeks in een buitensporig grote vormholte wordt geïnjecteerd, wat resulteert in grotere smeltbreuken en dienovereenkomstig grotere smeltsporen op het eindproduct.
De essentie van smeltbreuk is te wijten aan het elastische gedrag van polymeersmelten. Wanneer de smelt in het vat stroomt, wordt de smelt nabij de wand van het vat onderworpen aan wrijving, wat resulteert in hogere spanningen en een lagere stroomsnelheid. Zodra de smelt uit het mondstuk is geïnjecteerd, verdwijnt de spanning die wordt uitgeoefend door de vatwand en stroomt de smelt in het midden van het vat met extreem hoge snelheid. De smelt nabij de vatwand wordt gedragen en versneld door de centrale smelt. Omdat de stroom van de smelt relatief continu is, zullen de stroomsnelheden van de interne en externe smelten zich herschikken en naar een gemiddelde snelheid neigen.
Tijdens dit proces zal de smelt een scherpe verandering in spanning ondergaan, wat resulteert in spanning. Vanwege de extreem hoge injectiesnelheid is de uitgeoefende spanning bijzonder groot en overschrijdt deze het rekvermogen van de smelt ruimschoots, wat leidt tot het scheuren van de smelt.
Als de smelt plotselinge vormveranderingen in de runner tegenkomt, zoals vernauwing van de diameter, uitzetting of de aanwezigheid van dode plekken, blijft de smelt hangen en circuleert in deze dode plekken. De spanningsomstandigheden verschillen van die van de normale smelt, met grotere schuifvervorming. Wanneer het zich weer mengt in de normale stroom en wordt geïnjecteerd, kan het inconsistente vervormingsherstel tussen de twee niet met elkaar worden verzoend. Als de discrepantie significant is, treden breuken en breuken op. Dit fenomeen manifesteert zich ook als smeltbreuk.
Uit het bovenstaande is het duidelijk dat smeltbreuk moet worden overwonnen en het optreden van vlekken moet worden vermeden :
Ten eerste is het belangrijk om dode hoeken in het runnersysteem te elimineren om de stromingskanalen zo gestroomlijnd mogelijk te maken.
Ten tweede: verhoog op passende wijze de temperatuur van het materiaal om de relaxatietijd van het gesmolten materiaal te verkorten, waardoor het gemakkelijker wordt voor de vervorming ervan om te herstellen en te genezen.
De derde benadering is het toevoegen van stoffen met een laag molecuulgewicht aan de grondstoffen, omdat hoe lager het molecuulgewicht van de smelt en hoe breder de verdeling ervan, des te meer dit helpt de elastische effecten te verzachten.
De vierde is het op passende wijze regelen van de injectiesnelheid en de rotatiesnelheid van de schroef.
Ten vijfde is het van cruciaal belang om de locatie van de poort redelijk te bepalen en de juiste vorm van de poort te kiezen. De praktijk leert dat het gebruik van een vergrote puntpoort of een onderzeese poort (tunnelpoort) ideaal is. De beste locatie voor de poort is waar het gesmolten materiaal eerst een overgangskamer binnengaat voordat het in de grotere holte stroomt, in plaats van het materiaal rechtstreeks in de grotere holte te laten stromen.
2. Factor twee: Onjuiste controle over de vormomstandigheden
Dit is ook een belangrijke oorzaak van schroei- en brandplekken op het oppervlak van plastic onderdelen, vooral de omvang van de injectiesnelheid heeft een aanzienlijke impact. Wanneer het gesmolten materiaal langzaam in de vormholte wordt geïnjecteerd, is de vloeitoestand van de smelt laminair; naarmate de injectiesnelheid tot een bepaald niveau toeneemt, gaat de stromingstoestand geleidelijk over naar een turbulente stroming.
Onder normale omstandigheden heeft het oppervlak van kunststof onderdelen die onder laminaire stromingsomstandigheden zijn gevormd de neiging helder en glad te zijn, terwijl onderdelen die onder turbulente omstandigheden zijn gevormd niet alleen gevoelig zijn voor oppervlaktevlekken, maar waarschijnlijk ook luchtzakken in de onderdelen hebben. Daarom mag de injectiesnelheid niet te hoog zijn; het is raadzaam om de stroom van het materiaal te regelen om de mal in een laminaire toestand te vullen.
Als de temperatuur van de smelt te hoog is, kan dit gemakkelijk leiden tot ontleding en verkoling van de smelt, met als gevolg verbrande plekken op het oppervlak van de kunststof onderdelen. Over het algemeen moet de schroefsnelheid van een spuitgietmachine minder dan 90 tpm zijn en de tegendruk minder dan 2 MPa, om overmatige wrijvingswarmte in het vat te voorkomen.
Als er tijdens het gietproces overmatige wrijvingswarmte ontstaat omdat de rotatietijd van de schroef te lang is tijdens het terugtrekken, kan dit worden overwonnen door de schroefsnelheid op passende wijze te verhogen, de gietcyclus te verlengen, de tegendruk van de schroef te verminderen en de temperatuur van de toevoer te verhogen. gedeelte van de loop, en het gebruik van materialen met een slechte smering.
Tijdens het injectieproces kan een overmatige terugstroming van de smelt langs de schroefgroeven en het vasthouden van hars bij de terugslagklep leiden tot degradatie en ontleding van de smelt. Om dit aan te pakken, is het raadzaam om harsen met een hogere viscositeit te gebruiken, de injectiedruk op passende wijze te verlagen en over te schakelen naar spuitgietmachines met een grotere lengte-diameterverhouding. De terugslagkleppen die gewoonlijk in spuitgietmachines worden gebruikt, zijn zeer gevoelig voor retentie, wat leidt tot ontleding en verkleuring. Wanneer de ontlede en verkleurde smelt in de vormholte wordt geïnjecteerd, kunnen er theekleurige of zwarte brandvlekken ontstaan. Om dit te voorkomen moet het schroefsysteem rondom het mondstuk regelmatig worden gereinigd.
3. Factor drie: schimmelstoring
Als de ventilatiegaten van de mal geblokkeerd zijn door lossingsmiddelen of gestolde afzettingen van de grondstoffen, als de ventilatie-opstelling onvoldoende of onjuist gepositioneerd is, of als de vulsnelheid van de mal te snel is, kan de opgesloten lucht in de mal een adiabatische compressie ondergaan, waardoor er Gassen met hoge temperaturen die harsafbraak en verkoling kunnen veroorzaken. Om dit aan te pakken moeten verstoppingen worden verholpen, de klemkracht worden verminderd en de slechte ventilatie van de mal worden verbeterd.
Ook de bepaling van de vorm en positie van de matrijspoort is van groot belang. Tijdens het ontwerpproces is het noodzakelijk om volledig rekening te houden met de vloeitoestand van het gesmolten materiaal en de uitlaatprestaties van de mal.
Bovendien mag de gebruikte hoeveelheid lossingsmiddel niet overmatig zijn en moet het oppervlak van de vormholte met een hoge mate van gladheid worden gehandhaafd.
4. Factor vier: grondstoffen voldoen niet aan de eisen
Als de grondstoffen een te hoog gehalte aan vocht en vluchtige stoffen bevatten, of als de smeltvloei-index te hoog is, of als er een overmatige hoeveelheid smeermiddel wordt gebruikt, kan dit leiden tot schroeiplekken en brandplekken.
Hiervoor moeten grondstoffen worden behandeld met een hopperdroger of andere voordroogmethoden, overschakelen op harsen met een lagere smeltindex en de hoeveelheid gebruikt smeermiddel verminderen.